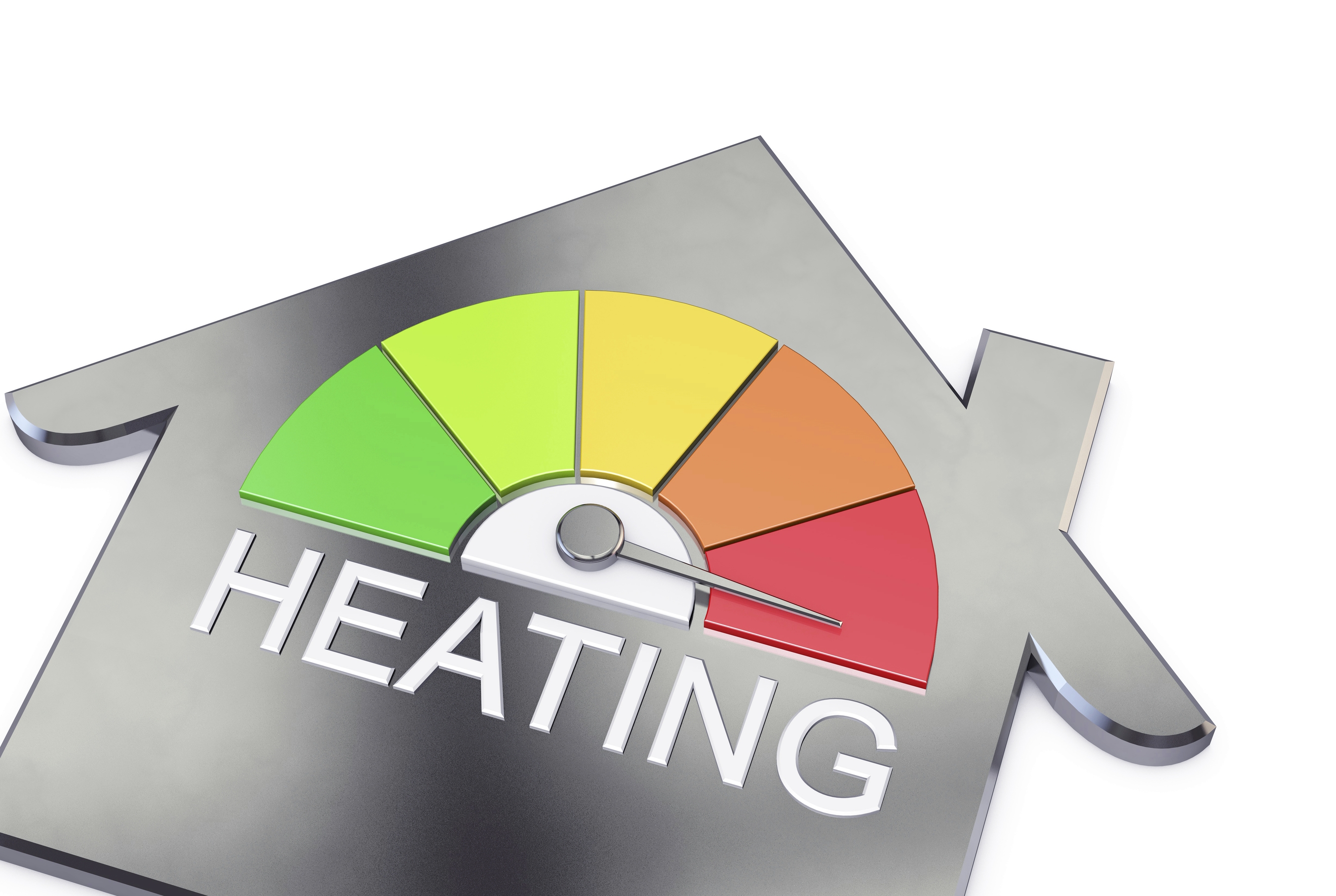
In this blog we will demonstrate how knowing how changes to the use or layout of your building impact on your building performance, energy consumption, while also dramatically effecting occupant comfort, helpdesk calls and productivity.
I would like to help you understand some of the typical issues we find when we work with our clients on a building energy reduction plan. Many of these issues are normally right in front of your eyes! You may be surprised to learn that many issues are created by the way a building is used, perhaps more accurately the way the use is changed without recourse to the HVAC system and the controls system.
We have discussed in previous blogs, the need to understand your buildings’ performance, from a fundamental level, how to engage your stakeholders, the first key practical steps we take on site and those user adjustments that affect building energy consumption.
Who put that there?
Our site surveys find surprisingly obvious physical issues with the layout of the office and/or the HVAC system. The survey, often involving our Controls Performance Report service (CPR) examines in detail, the core performance components of the building management system and provides a structured easy to use report that highlights where functional and operational issues lie.
Complemented by assessing the layout of the offices, the implementation of the HVAC systems and the feedback from the occupants, we build a strong picture of what is really happening within the building and establish causes for poor conditions and excessive energy consumption.
Recently, we were conducting a site survey and occupant review of a multi-storey office building in Central London. We started on the floors with the most issues in terms of complaints from staff. We discovered a number of problems had been created by the rearrangement of the office layout. Issues that meant the control and HVAC system were not be able to condition the new spaces created effectively.
One in particular was the creation of a number of small office rooms (approx. 10ft x 7ft) each with space for a single desk, two chairs, a coat stand and a small table. The three offices were built side by side within the existing office space.
Good so far? Well, the office at the end had severe problems. There was high airflow through it, so much so you could feel the cold air flowing past you and the individual in that office was really struggling with the cold. We noted a temporary solution standing on the floor of the office, an oil fired 3kw heater which was supplied in an attempt to help.
Can you see how things are stacking on top of each other to create a bigger issue?
Our investigations showed the first office to have only an extract grille, the second office had nothing and the third office – the biggest problem – had a supply grille. Bearing in mind the HVAC system had not been reconfigured during this office change, so the supply grille that was designed to pump air into a large open plan space but was pounding air into a small room. The controls for which were in the main space, which was hot – that’s another story! – So the main system was ‘trying’ to cool the whole floor space. The person in the small office with the large supply grille was being hit with air at 16 degrees!
Spotting these issues allowed us to advise on remedial work required for the HVAC configuration – in this case the change round of ducts from certain VAV units, and the implementation of local controls for the offices, means that the issues will be mitigated.
Going forward the client has altered their procedures to ensure that the BEMS team are engaged in office refits, to make sure this doesn’t happen again.
If issues like this sound familiar then you need our help and guidance. We can save you money, reduce operating costs, reduce staff complaints and improve productivity.
Conducting a site survey, a controls energy audit and Controls Performance Report will give you the information you need to make informed decisions and to help you take the next step.