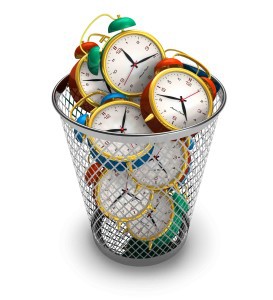
Did you know that by simply knowing how long a meeting will last can help you save energy consumption in your building?
We are going to start helping you understand some of the typical issues we find when working with clients on a building energy reduction plan.
In previous blogs we have discussed the need to understand your buildings’ performance from a fundamental level and not succumb to promises made in various glossy brochures. We’ve also looked at how to engage your stakeholders and how getting them to adopt your plan can help deliver your savings, operational and environmental targets.
Here at AIS BMS, we use dedicated tools which investigate the performance and operation of your building, using data from the BEMS and additional information such as ½ hourly meter readings. One of the typical discoveries we make is that the building is using excessive energy when it shouldn’t even be running. For example, over a weekend or overnight.
So let’s talk about real examples of real issues that we come across when analysing a clients’ building. You may be surprised to learn that many of these issues are actually created by the way the building is used and operated on a daily basis.
The most common cause we have seen for this is incremental user adjustments that are compounded over time. When a change is made to times or temperatures or plant being put into manual operation, the building responds, often in unexpected ways elsewhere, often causing feedback from the occupants that drives a temporary ‘fix’ to alleviate the issue. More often than not, this fix takes the form of an additional tweak or change that compounds the operational efficiency of the building further still.
The most common example being building operation time changes, those intended for a short period of time, an ad-hoc meeting in a certain part of the building perhaps, but the change never gets returned to ‘normal’.
We have recently been working with one of our clients in London and during our site survey and assessment of their building we identified excessive energy use over the weekend. Both Saturdays and Sundays were showing very high consumption all day. On further investigation, we found that the operational times had been changed, and in a way that made them continuous, not just an exception. So, every Saturday and every Sunday since the change, the building was using energy when it shouldn’t have been. The AHU’s were running, the boilers and chillers were enabled and working on a demand lead basis.
What was the reason for the changes in the first place?
A special meeting was being held in the office, and a request was made from the tenant to the FM team to have the building conditions at the right levels, which was a perfectly reasonable request. The changes were made to the operating times in the BEMS and the meeting went ahead as planned.
What did we discover?
The problem was that the changes made for the meeting were made incorrectly and became the normal setting, they never reverted back, creating an energy over consumption issue. Our survey was carried out in October 2015 and investigation into the log of the BEMS showed that the changes were made in September… 2014! We established that the changes were made in the wrong way due to operators not having sufficient knowledge in using the BEMS and that onsite training would be beneficial.
How much could have been saved?
The annual cost was estimated at over £7,000 in needlessly consumed energy.
What was the outcome?
The client is now reviewing their procedures and we have proposed a training and orientation course to help the operatives run the system more efficiently, having also made the required adjustments to the operating times while we were on site.
This is just one simple example of how building performance suffers over time through a series of adjustments, fixes and changes to the operational parameters in the controls system.
Running a full controls energy audit and taking advantage of our Controls Performance Report will give you all the information you need to spot these issues, make informed decisions and to help you take the next steps. These tools dig deep into the very operational heart of your Building Energy Management System and highlight areas for improvement.
If you are responsible for a building, or a portfolio of buildings, you need to ask yourself if you can afford not to take this step. Contact us to find out more on our simple but effective methods that will help you drive energy waste out of your building and improve operational availability and reliability.